Schwarzach, Austria
Schwarzach Packaging
Since its foundation in 1913, Schwarzach Packaging GmbH has become established as a supplier of packaging solutions for the international consumer goods industry. At the Schwarzach site in the west of Austria, around 300 employees process 20,000 tons of cardboard and paper a year. In 2009, the company was one of the first packaging manufacturers in Europe to implement the natureOffice standard for climate-neutral printing: the CO2 emission values are continuously calculated for each print job. The more environmentally friendly the organization of the production chain – from cardboard production to logistics – the lower the compensation amount.
PROJECT OVERVIEW
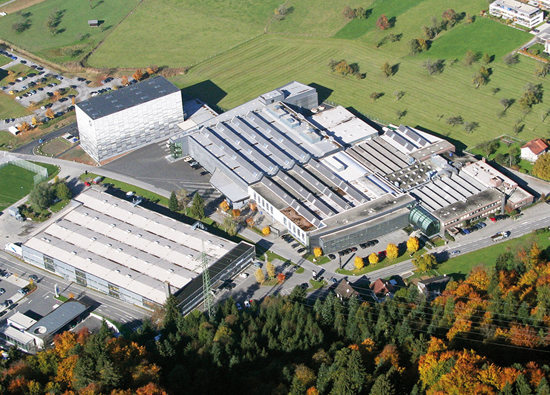
The double production capacity demands a new and fully automatic logistics center. The management board of Schwarzach Packaging therefore plan the most ambitious expansion since the company was founded. One thing is certain: climate protection is seen as a responsibility throughout the company – as well as a market strategy. The objective and scale of this is geared to securing a certificate for climate-neutral printing. Having such a logo on your packaging creates confidence, and with it, a competitive edge.
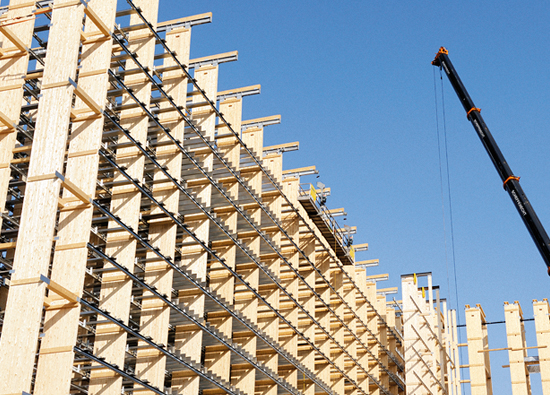
It becomes clear during the planning stage that the building material has to be wood – this was the only way to achieve a CO2 reduction of an astonishing 880 tons. Local spruce wood is also a renewable resource that does not have to travel far. And although the price of steel falls considerably during the planning phase, the added ecological value of wood ultimately outweighs the marginal additional charge. In any case, the extremely short construction period of just five months from the time the contract is awarded is only feasible if the building material is wood.
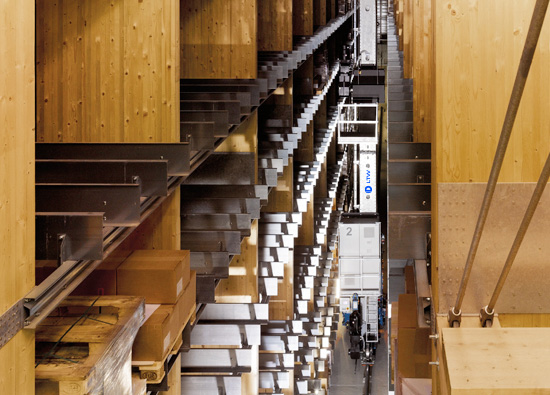
The energy-saving design of the intralogistics solution proposed by LTW contributes to the excellent CO2 balance sheet of Schwarzach Packaging. The weight-optimized design of all three stacker cranes, route optimization – a few new features are added to the current eco-standard at LTW. LTW takes advantage of the fact that every downward movement of the lifting carriage releases energy. This is converted into electricity and fed back to the grid.