Latsch, Italy
Mivor
In March 1954, 12 farmers from Latsch create the "Mittelvinschgauer Obsterzeugergenossenschaft" fruit producers' cooperative, or MIVO for short. Its rapid success brings a response in 1960: the creation of a second Latsch cooperative Ortler, named after the highest mountain in South Tyrol. In 1979, competition between the two cooperatives gradually comes to an end. This is followed in 2007 by the merger that forms MIVOR. Today, the 400 members of MIVOR produce around 500 million apples on 1,100 hectares of cultivated land every year. Nearly half of this is exported to a total of 49 countries in Europe, North Africa, and Asia.
PROJECT OVERVIEW
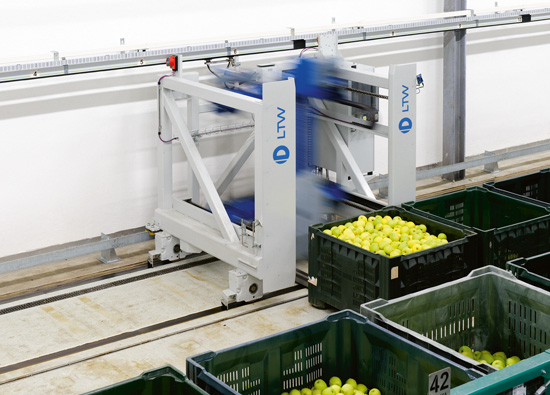
Greatly improved farming methods and yields on the one hand, and increased international competition on the other, motivate the seven local cooperatives of the South Tyrolean fruit growing region of Vinschgau to centralize the marketing of their fruit in the umbrella organization VI.P. However, the responsibility for keeping production as efficient as possible still lies with the individual cooperatives. Two of them, the former rivals MIVO and Ortler, merge to become Europe's biggest fruit processing operation MIVOR. Shortly after the merger, the planning committee tackle the issue of storage.
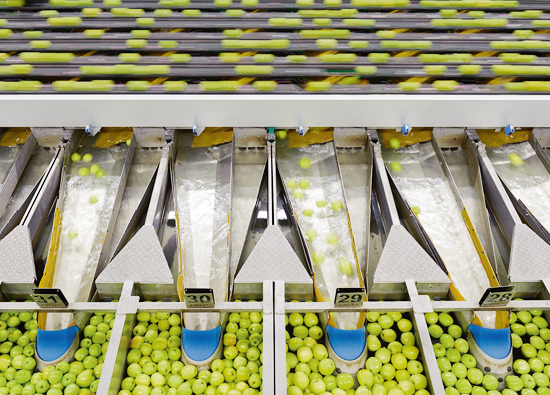
Part one of the project is an innovative sorting system, developed by MIVOR together with a specialist. Important findings from this process are included in part two of the project: an automatic high-bay warehouse to be erected in the middle of the densely built-up area. There are only a few providers who even dare to accept this technological challenge. The LTW concept ultimately emerges victorious from a fastidious and complex scoring system.
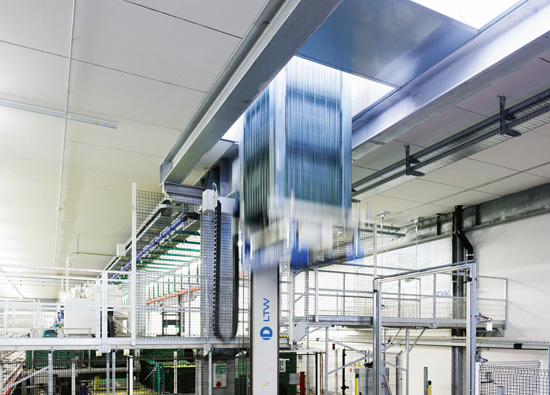
The fruit processing cycle in Latsch is dictated by the seasons. During the apple harvest in September, more than 300,000 bins of apples are cooled to 2 °C in a very short time. Oxygen-reduced CA cells (controlled atmosphere) allow long-term storage without loss of freshness. In the course of the year, the entire harvest is gradually worked through, which means sorted and packaged by size, color, and quality. The high-bay warehouse comes into play as a buffer between the sorting system and the packaging hall. In contrast to normal stacking operations, the six stacker cranes in use here apply the FIFO principle (First In, First Out). This results in a freshness benefit of up to a week!