Feldkirch, Österreich
Bischof Lebensmittellogistik
Die Entwicklung des Vorarlberger Logistikdienstleisters ist eng verknüpft mit der expandierenden Lebensmittelindustrie der Region. Für Kunden wie Kraft Foods, 11er, Hilcona, Bofrost und Ölz realisiert Bischof eine umfassende Leistungskette: von der Abholung der tiefkühl- und temperaturgeführten Lebensmittel über die Verzollung, Lagerung, Kommissionierung und Konfektionierung bis hin zum Co-Packing, der Auslagerung sowie der termingerechten Lieferung an Großhandelsketten und Einzelhändler in ganz Europa. Das Rückgrat der Kühlkette bilden derzeit 260 Mitarbeiter, 190 Kühlzüge und 25.000 Palettenplätze, davon 16.000 im Tiefkühlbereich.
PROJEKTÜBERBLICK
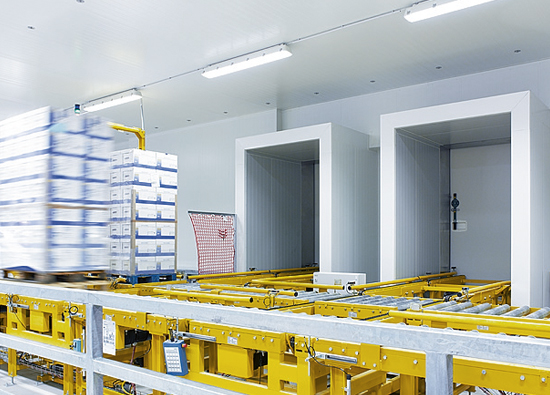
Bischof entschließt sich dazu, die Lagerkapazität zu verdoppeln und ein vollautomatischen Tiefkühl-Hochregallager zu bauen. Wichtige Kunden, darunter 11er und Kraft Foods, signalisieren die kräftig steigende Nachfrage und liefern auch gleich eine Empfehlung für die Umsetzung: LTW Intralogistics! Dank der ausgezeichneten Referenzen im Tiefkühlbereich erhält LTW den Zuschlag für die Lieferung der Regalbediengeräte, Fördertechnik und Lagerverwaltungssoftware.
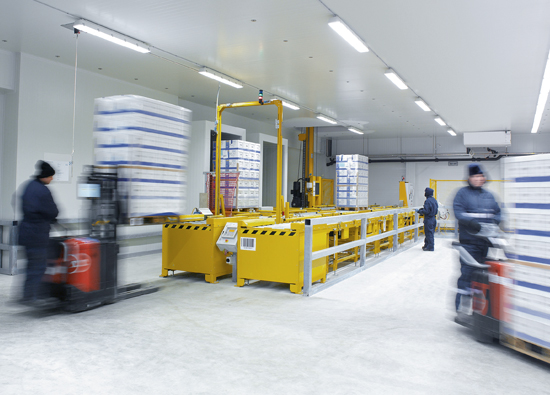
Der vollautomatische Betrieb einer Logistikanlage bei -28 °C im Hochregallager und -5 °C in der Vorzone stellt hohe Ansprüche an die Planung und Ausführung der Geräte dar. Erfahrung ist gefordert, um das Schrumpfverhalten der verwendeten Materialien richtig einschätzen zu können und um auf wichtige Details zu achten – vom kältetauglichen Getriebeöl bis zu beheizbaren elektrischen Komponenten.
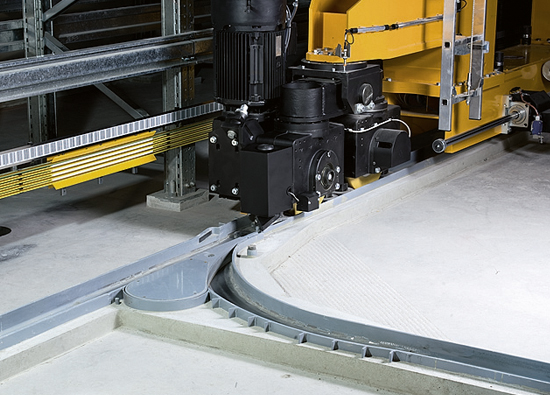
Der Warenfluss im 4-gassigen, doppeltiefen Hochregallager wird durch zwei weichengängige Regalbediengeräte realisiert – Kollisionen werden durch das LTW-Lagerleitsystem ausgeschlossen. Jede Regalgasse ist im Stirnbereich an die Fördertechnik angeschlossen. Zwei Verschiebewagen schlagen die Brücke zur Einlager- bzw. Auslagerstrecke. Ein Vertikalförderer bindet den Kommissionierbereich im Obergeschoss an den Materialfluss an. Features wie Konturenkontrolle und Pufferplätze sichern den reibungslosen Betrieb.